With the increasing use of robotics, the traditional teaching methods of teaching programming have become very inefficient in some occasions, so offline programming has emerged and applications have become more and more popular. However, friends who use offline programming at first will always be confused by the error of the last generated trajectory, and the causes of these errors include the TCP mentioned in the previous issues, the accuracy of the workpiece, and the other, that is, the absolute positioning error of the robot. .
Below we summarize the sources of error in off-line programming and how to minimize these errors.
[Error Source 1: TCP Measurement Error]
First of all, we must talk about TCP. I think the friends of Xiaomeng’s article are familiar with this. TCP is the center of the tool. If the robot does not find the center of the tool it is holding, you can imagine how big the error is. So we have to measure TCP. After the measurement, we need to control the error within the approved range, and then verify the measurement results. We can perform the relocation operation at the fixed point to check the robot's multi-pose motion at the fixed point. Whether it is within the specified error range.
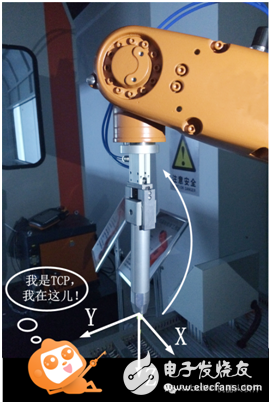
This puts requirements on the offline programming software. In the offline programming software, the real TCP of the measurement can be input. These necessary functions are basic functions in the first-line brands such as RobotArt and RobotMaster.
[Error Source 2: Workpiece Geometry and Positioning Error]
The second is the workpiece error, there are two aspects:
On the one hand, the error of the workpiece model is essentially to ensure that the size of the virtual model in the offline programming environment is exactly the same as in the real world. Therefore, it is necessary to improve the accuracy of the workpiece to reduce the error caused by the workpiece itself.
The other is the error in the position of the workpiece. Taking the domestic offline programming software RobotArt as an example, the “workpiece calibration†function provided in the software is to eliminate this error. The workpiece calibration done by the three-point method can meet the basic accuracy requirements. For high-precision applications, in order to reduce the error of the workpiece position, we can not only measure three points, but we can also measure multiple points on the workpiece so that the error can be further reduced. This feature RobotArt is much more useful than RobotMaster, and it is a good idea for domestic software!
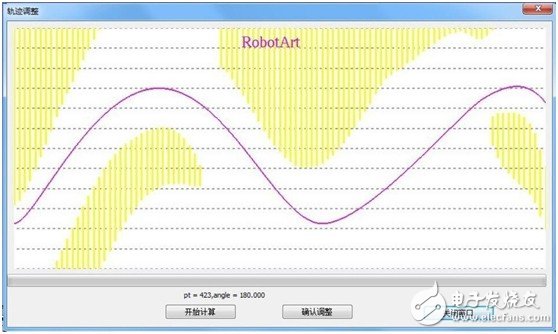
[Error Source 3: Robot Assembly and Absolute Positioning Error]
Finally, there are robot errors, and there are two aspects:
On the one hand, the error caused by the robot itself during the processing and assembly process, which leads to the final generated robot, which may not be exactly the same as the DH parameter when designing, just as there are no two identical leaves in the world, the world There are also no two identical robots.
The other hand is the absolute positioning error of the robot. All robot manufacturers have not told you a fact. Among the nominal parameters disclosed by the major robots, the repeatability is repeated, which can reach 0.05mm, or 0.02mm, but there is no one that provides absolute positioning accuracy. Absolute precision refers to the degree to which the actual value agrees with the theoretical value. We control the robot to move to each target point, and there is a certain distance error between the actual arrival point of the robot and the target point. For example, in the figure below, we give the same coordinates X, Y, and Z, and let the robot point to it three times in different postures. The result is that it is not reliable, so that Xiaomeng’s adoration of the robot was broken. Ground. But the situation is not so bad. This absolute error is only large in the attitude of the robot's limit. In the comfortable posture, the error is relatively small, and it is also different because of "people."
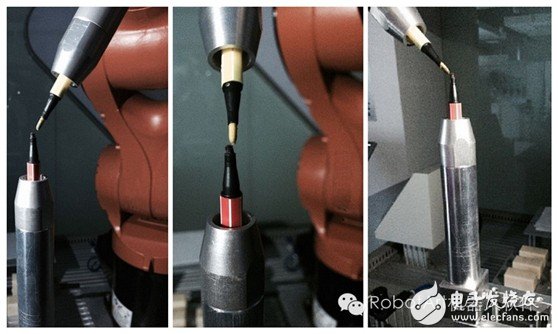
In the RobotArt offline programming software, this problem has been "accommodated", that is, in the trajectory optimization, the trajectory posture will be optimized to the "comfortable" position, and the secondary positioning method is provided to fully utilize the repeated positioning accuracy. And other means to try to eliminate this error. The following figure is the trajectory optimization function of RobotArt. By adjusting the trajectory analysis curve, the smoother the trajectory analysis line, the more "comfortable" the robot pose, and the smaller the absolute positioning error generated by the robot body.
By eliminating the above three sources of error, the accuracy of offline programming can be greatly improved, so that the robot can be well applied to complex trajectory fields such as grinding, deburring, cutting, and spraying. As the first domestic branded robot offline programming software, RobotArt has completely broken the monopoly of foreign software, greatly reducing the cost of domestic robot applications, and providing better services for domestic robot applications. We expect the Chinese to make more excellent offline programming software like RobotArt.
Below we summarize the sources of error in off-line programming and how to minimize these errors.
[Error Source 1: TCP Measurement Error]
First of all, we must talk about TCP. I think the friends of Xiaomeng’s article are familiar with this. TCP is the center of the tool. If the robot does not find the center of the tool it is holding, you can imagine how big the error is. So we have to measure TCP. After the measurement, we need to control the error within the approved range, and then verify the measurement results. We can perform the relocation operation at the fixed point to check the robot's multi-pose motion at the fixed point. Whether it is within the specified error range.
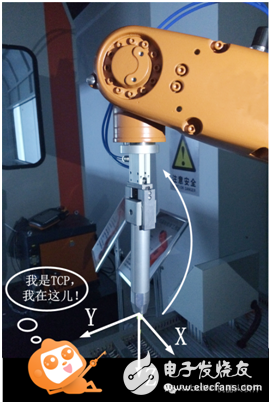
This puts requirements on the offline programming software. In the offline programming software, the real TCP of the measurement can be input. These necessary functions are basic functions in the first-line brands such as RobotArt and RobotMaster.
[Error Source 2: Workpiece Geometry and Positioning Error]
The second is the workpiece error, there are two aspects:
On the one hand, the error of the workpiece model is essentially to ensure that the size of the virtual model in the offline programming environment is exactly the same as in the real world. Therefore, it is necessary to improve the accuracy of the workpiece to reduce the error caused by the workpiece itself.
The other is the error in the position of the workpiece. Taking the domestic offline programming software RobotArt as an example, the “workpiece calibration†function provided in the software is to eliminate this error. The workpiece calibration done by the three-point method can meet the basic accuracy requirements. For high-precision applications, in order to reduce the error of the workpiece position, we can not only measure three points, but we can also measure multiple points on the workpiece so that the error can be further reduced. This feature RobotArt is much more useful than RobotMaster, and it is a good idea for domestic software!
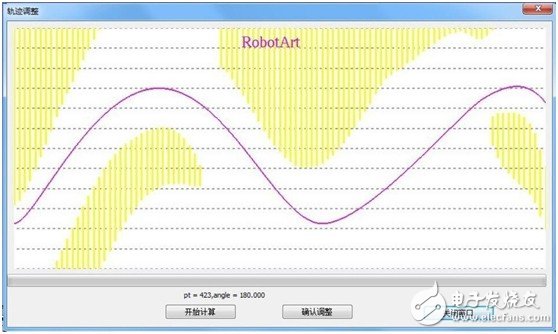
[Error Source 3: Robot Assembly and Absolute Positioning Error]
Finally, there are robot errors, and there are two aspects:
On the one hand, the error caused by the robot itself during the processing and assembly process, which leads to the final generated robot, which may not be exactly the same as the DH parameter when designing, just as there are no two identical leaves in the world, the world There are also no two identical robots.
The other hand is the absolute positioning error of the robot. All robot manufacturers have not told you a fact. Among the nominal parameters disclosed by the major robots, the repeatability is repeated, which can reach 0.05mm, or 0.02mm, but there is no one that provides absolute positioning accuracy. Absolute precision refers to the degree to which the actual value agrees with the theoretical value. We control the robot to move to each target point, and there is a certain distance error between the actual arrival point of the robot and the target point. For example, in the figure below, we give the same coordinates X, Y, and Z, and let the robot point to it three times in different postures. The result is that it is not reliable, so that Xiaomeng’s adoration of the robot was broken. Ground. But the situation is not so bad. This absolute error is only large in the attitude of the robot's limit. In the comfortable posture, the error is relatively small, and it is also different because of "people."
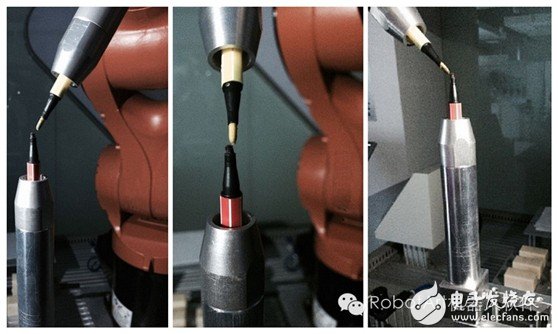
In the RobotArt offline programming software, this problem has been "accommodated", that is, in the trajectory optimization, the trajectory posture will be optimized to the "comfortable" position, and the secondary positioning method is provided to fully utilize the repeated positioning accuracy. And other means to try to eliminate this error. The following figure is the trajectory optimization function of RobotArt. By adjusting the trajectory analysis curve, the smoother the trajectory analysis line, the more "comfortable" the robot pose, and the smaller the absolute positioning error generated by the robot body.
By eliminating the above three sources of error, the accuracy of offline programming can be greatly improved, so that the robot can be well applied to complex trajectory fields such as grinding, deburring, cutting, and spraying. As the first domestic branded robot offline programming software, RobotArt has completely broken the monopoly of foreign software, greatly reducing the cost of domestic robot applications, and providing better services for domestic robot applications. We expect the Chinese to make more excellent offline programming software like RobotArt.
Active Stylus Pen,Stylus Pencil,Capacitive Stylus Pen,Tablet Pencil
Shenzhen Ruidian Technology CO., Ltd , https://www.wisonen.com