Fifty years ago, process control was based on a 3 to 15 psi pneumatic signal standard base-type pneumatic control instrumentation system (PCS, PneumaTIc Control System), the first generation of process control architecture; based on analog current signal standard 0~10mA (4~20) mA) The electric unit combined analog instrumentation control system (ACS) is the second generation process control architecture; in the 1970s, due to the use of digital computers, a centralized digital control system (CCS, ComputerControl System) is the third generation process control architecture; in the 1980s, the emergence and application of microprocessors led to the creation of a Distributed Control System (DCS), the fourth generation of process control architecture; In the 1990s, the emergence of fieldbus technology led to a new generation of process control architecture, the Fieldbus Control System (FCS).
Definition and main points of DCS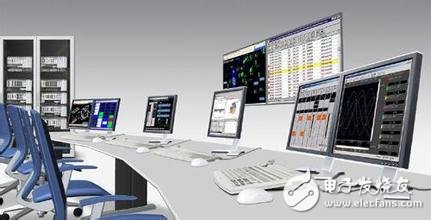
Distributed Control System (Distributed Control System), also known as computer distributed control system, was developed rapidly in the mid-1970s. It is a multi-level computer with communication network as the link between process control level and process monitoring level. The system combines control technology, computer technology, image display technology and communication technology to achieve monitoring, control and management of the production process. It not only breaks the limitations of the conventional control instrument function, but also better solves the danger of the early computer system's excessive concentration of information, management and control. It is mainly used in large-scale continuous process control systems, such as petrochemicals and electricity. At its core is communication, the data highway.
Its basic points are:
(1) Tree system from top to bottom, where communication is key.
(2) PID is in the interrupt station, the interrupt station is connected to the computer and the field instrumentation and control equipment. ;
(3) It is a tree topology and a parallel continuous link structure. There are a large number of cables from the relay station in parallel to the field instrumentation.
(4) The signal system includes a binary signal and an analog signal.
(5) DCS is a three-level structure of control (engineering station), operation (operator station), and field instrument (site monitoring station).
Definition and main points of FCS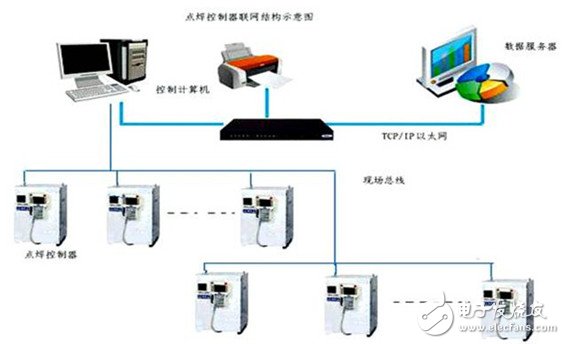
Fieldbus Control System (FCS) is a fieldbus control system. It uses fieldbus as an open, interoperable network to interconnect various controllers and instruments and instrumentation devices on site to form a fieldbus control system and control functions. Decentralized to the site, reducing installation costs and maintenance costs. Therefore, FCS is essentially an open, interoperable, and thoroughly distributed distributed control system that is expected to become the mainstream product of the 21st century control system. The core of the fieldbus control system is the bus protocol. The foundation is digital intelligent field devices, which is essentially the on-site processing of information processing.
The main points of FCS are:
(1) FCS is a fusion of 3C technology (CommunicaTIon, Computer, Contro1). It applies to the essential (intrinsic) safety, hazardous areas, volatile processes, and very difficult environments to deal with.
(2) Field devices are highly intelligent, providing full digital signals; one bus connects all devices.
(3) The two-way digital communication bus from the control room to the field device is an interconnected, two-way, serial multi-node, open digital communication system that replaces the one-way, single-point, parallel, closed analog system.
(4) The control function is completely dispersed.
The difference between DCS and FCS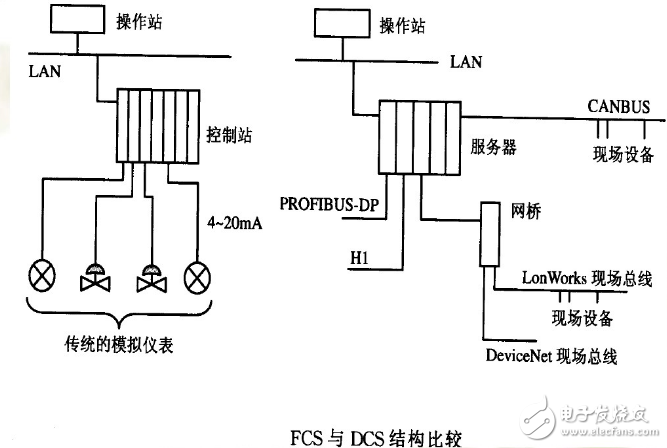
1. The DCS system is closed, and the products of each manufacturer are not compatible with each other; FCS is a fully open system, and its technical standards are also fully open. FCS field devices are interoperable and devices are compatible with each other, so users can choose different manufacturers. Different brands of products are connected to the same field bus at the same time to achieve optimal system integration.
2. The DCS system is a large system. The function of the controller is very important and the role in the system is very important. The data highway is the key to the system. Therefore, the overall investment must be in one step, and the expansion afterwards is difficult. The FCS function is released. More thorough, on-site information processing, the widespread adoption of digital intelligent field devices, the controller function and importance are relatively weak. Therefore, the FCS system has a low starting point for investment, and can be used while expanding, while operating.
3, FCS signal transmission is fully digital, its communication can be from the lowest level of sensors and actuators to the highest level, providing strong support for enterprise MES and ERP, more importantly, it can also remotely field devices Diagnostics, maintenance and configuration; DCS communication function is very limited, although it can also be connected to the Internet, but it can not connect to the bottom layer, it provides a limited amount of information, it can not remotely operate the field device.
4. The structure of the FCS is fully decentralized. It discards the I/O units and control stations in the DCS, and decentralizes the control functions to the field devices, achieving complete dispersion and system expansion. The DCS dispersion is only At the controller level, it emphasizes the function of the controller, and the data highway is the key.
5. The signal system of DCS is binary or analog. It must have A / D and D / A links, so its control accuracy is 0.5%. FCS is fully digitized. The control system has high precision and can reach 0.1% of soil. And the FCS system can install the PID closed-loop control function into the field device, shortening the control cycle and increasing the operation speed, thereby improving the adjustment performance.
6. The FCS can put the PID closed-loop function into the transmitter or actuator in the field, plus digital communication, so the sampling and control cycle is shortened. It can be increased from 2-5 times per second to 10 times per second from DCS. -20 times, thus improving the adjustment performance.
7. FCS is simpler to configure than DCS. Due to the standardization of structure and performance, FCS saves a lot of installation and debugging costs because it saves a lot of hardware equipment, cable and cable installation auxiliary equipment, so its cost is much lower than that. DCS.
For example, the application of continuous steel casting process in DCS and FCS.
Contact between DCS and FCS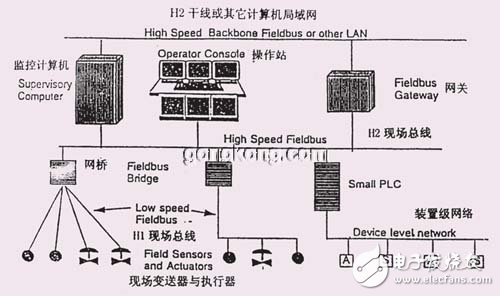
FCS is developed from PLC or DCS, and now FCS systems have been widely used. In the future, in industrial process control systems, digital technology will be developed towards intelligence, openness, networking, and information. At the same time, industrial control software will also be standardized, networked, intelligent, and open. The emergence of the fieldbus control system FCS, digital decentralized control DCS and PLC will not die, DCS and PLC systems will be more intelligent, open, networked, information development. The future control system will be: FCS is at the center of the control system, and has a new standardization, intelligent, open, networked, and informationized control system for DCS and PLC systems.
Digital communication is a trend that represents technological advancement that no one can stop. The two-way digital communication fieldbus signal system and the huge driving force generated by it accelerate the revolution of field devices and control instruments, and develop more and more fully functional digital intelligent field devices. These are not available in the DCS system, and the resulting advantages and benefits for the design, configuration, configuration, operation, maintenance, and management of thermal power plants are also beyond the reach of the DCS system. Furthermore, FCS was developed from DCS and PLC, which retains the characteristics of DCS, or FCS absorbs DCS's years of development research and field practice experience, including lessons. From this, it is concluded that "FCS will replace DCS" seems to be a matter of course.
At the same time, we should also see that the DCS system has been developed for nearly 30 years and is widely used in thermal power plants. Its design idea, configuration configuration, function matching, etc. have reached a very perfect level (of course, DCS also has further development needs, such as advanced software development to meet the requirements of information integration), has penetrated into the thermal power plant control system It is also reflected in various fields and in the FCS system. From this perspective, the DCS system does not seem to say that it has died. Furthermore, the DCS system still has a place for those areas where the FCS system cannot fully utilize its features and advantages. Just like the current DCS and the new PLC, due to years of development and research, they retain their original features and complement each other to form a new system. Now the DCS is not the original DCS. The same is true, the new PLC is also It is not the PLC at the beginning of development. Can we say that DCS has replaced PLC or PLC replaced DCS? Obviously it is not appropriate.
in conclusionFrom the above analysis, we can draw the following simple conclusion: the emergence of the fieldbus control system FCS, the digital decentralized control DCS will not die, but just move the DCS that was in the center of the control system to the fieldbus. Go to the site. It can also be said that the situation in which DCS is at the center of the control system will be broken. In the future, the control system of a thermal power plant will be: FCS is at the center of the control system and has a new control system with the DCS system philosophy.
An electronic clock device with a wireless network monitoring camera is characterized in that it comprises an electronic clock device body with a wireless network monitoring camera; the electronic clock device body with a wireless network monitoring camera is composed of a foot, a wireless transmission module, a It consists of a rechargeable battery, a speaker, a touch display screen, a camera, a casing, an infrared device, and a microprocessor; the feet are fixedly installed at the bottom of the rechargeable battery; a casing is fixedly installed on the top of the rechargeable battery, and the The interior is provided with a touch screen, a camera, an infrared device and a microprocessor; the microprocessor is electrically connected to the rechargeable battery through wires; the wireless transmission module, speaker, display, camera and infrared device are connected to the micro processor through wires The display screen is arranged at the bottom of the camera, and the camera is surrounded by an infrared device; the wireless transmission module is fixedly installed on both sides of the rechargeable battery, and the speakers are opened on both sides of the casing
Wifi Electronic Clock,Wifi Electronic Clock hidden camera,hidden camera wifi,hidden camera wireless,spy camera wifi
Jingjiang Gisen Technology Co.,Ltd , https://www.jsgisentec.com