1,
Pig’s trotters are commonly packaged in vacuum-sealed bags. The bones inside can exert puncture force on the packaging, and if the material lacks flexibility, it may result in pinholes or ruptures, leading to spoilage. Aluminum-plastic composite films often include aluminum foil, which is brittle and prone to developing pinholes or creases during production or transport. These defects can significantly reduce the package’s barrier and mechanical properties. To ensure product quality and extend shelf life, meat processing companies should conduct thorough barrier property tests on packaging materials before and after packaging.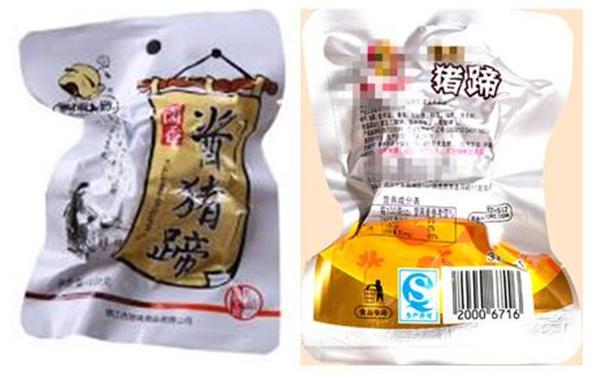
Figure 1: Pig’s trotters aluminum-plastic composite film packaging
2,
In China, common standards for testing oxygen permeability of flexible packaging include the differential pressure method and the coulomb method (equal pressure method). The GB/T 1038 standard outlines the differential pressure method, while GB/T 19789 describes the coulomb method. However, there is no specific standard for evaluating flexibility. Therefore, this study refers to ASTM F392 to simulate real-world damage such as folding and crushing that aluminum-plastic films may experience during production and transportation. The anti-fouling performance is assessed by measuring changes in barrier properties before and after the test.3,
Test Sample: An aluminum-plastic composite film provided by a milk powder factory was used for the experiment.4,
Test Equipment: The FDT-02æ‰æ“ tester and VAC-V2 differential pressure gas permeation instrument, both developed by Jinan Languang Electromechanical Technology Co., Ltd.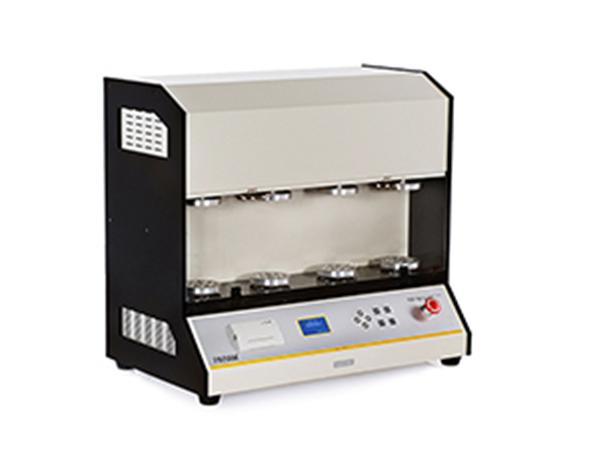
Figure 2: FDT-02æ‰æ“ tester
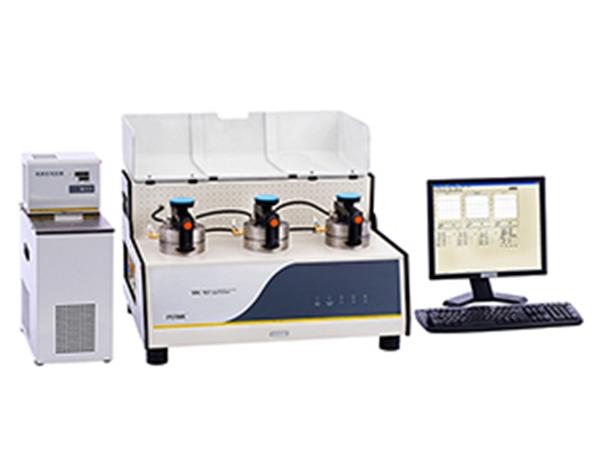
Figure 3: VAC-V2 differential pressure gas permeation instrument
4.1 Test Principle
The VAC-V2 uses the differential pressure method. After pre-treatment, the sample is placed between two chambers. The lower chamber is evacuated, then the upper chamber is filled with gas under pressure. A constant pressure difference is maintained across the sample, allowing gas to permeate from high to low pressure side. The pressure change in the low-pressure chamber is monitored to calculate permeation rates and other barrier parameters.4.2 Scope of Application
(1) Suitable for gas permeability testing of various packaging films, including plastic films, paper-plastic composites, co-extruded films, aluminized films, and more. (2) Applicable for testing gases like oxygen, carbon dioxide, nitrogen, and others, as well as flammable and explosive gas barriers. (3) Complies with international standards such as ISO 15105-1, ISO 2556, GB/T 1038, ASTM D1434, JIS K7126-1, and YBB 00082003.4.3 Equipment Parameters
- Test range: 0.05 ~ 50,000 cm³/m²·24h·0.1MPa - Number of samples: 3 (independent data) - Temperature: 5°C ~ 95°C, ±0.1°C accuracy - Humidity: 0% RH ~ 100% RH, ±1% RH accuracy - Supports temperature-dependent data fitting and Lystem™ lab data management system.4.4 Sample Preparation Process
- Cut Φ 97 mm samples using a sampler. - Cut three 280x200 mm samples and fix them on the FDT-02 with double-sided tape. - Use theæ‰æ“ mode for testing. - Repeat the process for subsequent samples.5. Test Procedure
(1) Test oxygen transmission rate before and after flexibility testing using VAC-V2. (2) Set sample name, thickness, temperature, and humidity. (3) Start the vacuum pump. (4) Click “Start Test†to begin the process; the system automatically calculates and displays results.6. Test Results
The average oxygen transmission rate of the tested sample was 2.9447 cm³/m²·24h·0.1MPa. After the test, the rate increased to 15.9022 cm³/m²·24h·0.1MPa, indicating potential damage during handling.7. Conclusions
The increase in oxygen transmission rate suggests that the aluminum-plastic film may have developed small pinholes or creases during packaging and distribution. Regular testing of oxygen permeability helps ensure product shelf life. The VAC-V2 is a reliable and accurate tool for measuring gas permeability, and when paired with the FDT-02, it effectively evaluates the flexibility, barrier properties, and sealing performance of packaging materials.Labthink
Languang has been dedicated to providing professional testing equipment and services globally, helping customers gather essential data on packaging material performance.The etching plate heat exchanger sheet is specifically used in the plate heat exchanger to isolate the media and heat exchange plate, is an important part of the plate heat exchanger. The quality of the plate heat exchanger plate affects the overall performance and working condition of the plate heat exchanger. The main materials we use in plate heat exchanger sheet are stainless steel, titanium and titanium-palladium.
Half Etching Metal plates thin metal plates with corrugations, sealing grooves and angular holes, which are important heat transfer elements. Corrugation can not only strengthen the heat transfer and can increase the rigidity of the thin plate and thus improve the pressure-bearing capacity of the plate heat exchanger, and as a result of the liquid is turbulent, it can reduce the formation of sediment or dirt, play a certain "self-cleaning" role.
We custom plate heat exchanger sheet with drawings provided by customers. We are equipped with professional metal etching equipment and exposure development equipment. We can guarantee that our half etching plate heat exchanger sheet have straight surface line, and have no burr, high product accuracy.
Etching Plate Heat Exchanger Sheet,Custom Plate Heat Exchanger Sheet,Half Etching Metal Plates,Half Etching Plate Heat Exchanger Sheet
SHAOXING HUALI ELECTRONICS CO., LTD. , https://www.cnsxhuali.com